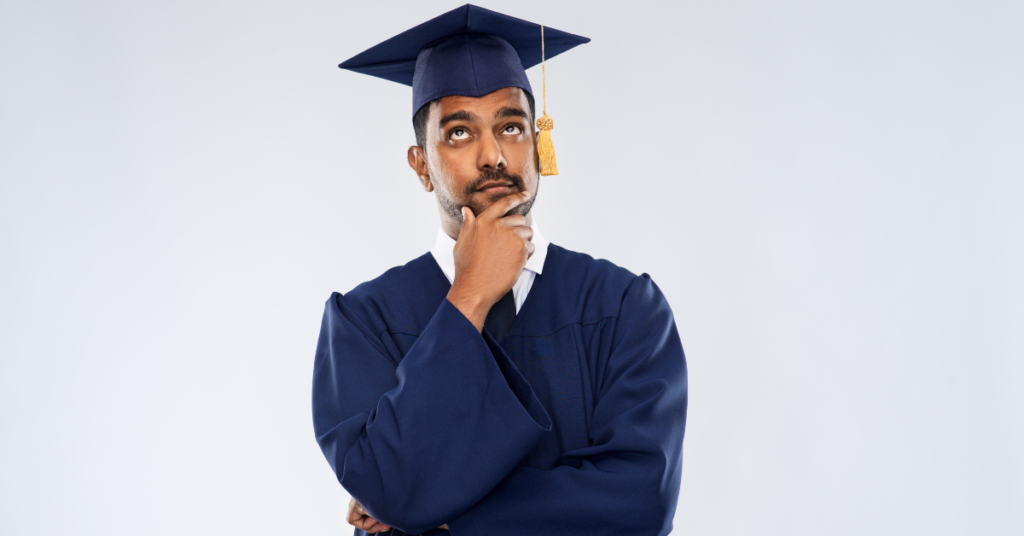
WHAT IS LEAN?
Lean is a philosophical way of working used to detect and eliminate waste in a process based on customers’ perspectives[1,2]. This includes variability and uncertainty involving supply, demand, and time. For instance, prolonged waiting times, delays, defects/errors, and storing and inspecting data – all do not add value that customers are not willing to pay for[3].
Derived from the Toyota Production System (TPS) by the Toyota Motor Corporation, Lean’s ultimate objective is to design a smooth process of high quality that can produce completed products or provide service that can meet customers’ expectations and enhance satisfaction without waste (delays, interruptions, bottlenecks, etc.)[1,4].
WHAT IS WASTE?
Waste is any Non-Value-Adding (NVA) activity that;
- Does not transform raw material to finished goods or order/raw information to serviceability
- Customer is not willing to pay for it
- Business does not require it
In Lean, waste comes in seven different forms which are time, inventory, motion, waiting, overproduction, overprocessing, and defects (TIMWOOD) – a.k.a. Lean’s 7 Deadly Waste. Yet, in recent years, another form of waste was discovered which is ‘skill sets’ (non-utilized talent); hence, making it the 8 Lean Wastes or TIMWOODS.
THE 5 KEY PRINCIPLES OF LEAN
Implementation of Lean enables organizations to function more efficiently with less space, time, and resources, focuses more on the quality of the value creation for the customers, assists organizations to achieve operational excellence, and provides techniques and tools to obtain continuous improvement within their operations[2,3]. Ultimately, Lean shapes an organization’s philosophy and therefore allows organizational, behavioural, and cultural transformation within the organization[3].
To achieve this, 5 key Lean principles were proposed by Jones and Womack (1990) to provide a framework for Lean implementation[5]. These principles are;
1. Identify Value
Value is the needs of customers in a product or service that they are willing to pay for. It is vital for an organization to determine customers’ actual or latent needs to ensure that the operations/processes executed to meet customers’ needs and expectations are optimized[6]. Understanding the needs of customers can be accomplished by consulting customers (existing or potential) via interviews, surveys, web analytics, and so on[7].
Identifying customer value leads to discovering customers’ wants, how products or services should be provided, and the price customers are willing to pay. Thus, it helps an organization achieve continuous improvement within the processes of meeting these values and expectations.
2. Map Value Stream
Upon identifying the value, mapping the value stream is the next step. This involves investigating activities within a process that are either value-adding or non-value-adding. This is done by creating a diagram that helps visualize the process flow of the value within the organization. To illustrate, this diagram or ‘map’ identifies each task/activity carried out to produce, deliver, or provide a product or service through a process – be it in design, manufacture, delivery, production, or customer service processes[7,8].
The goal of mapping the value stream is to identify only actions that contribute to the customers’ value. Those that do not add value are considered waste and ways to eliminate them are investigated. This principle provides a clear way to enhance process efficiency in producing value for customers as well as understanding the entire business operation. Reducing and eliminating non-value-adding activities within the processes can reduce production costs and ensure customers’ satisfaction after receiving products/services that they want and are willing to pay for.
3. Create Flow
Once the flow of the value is well understood, creating a smooth-running value chain – from production to delivery of product/service to the customer – without interruptions, delays, or bottlenecks is the next step. When the value stream stops, wastage is the by-product. Thus, every activity done in a value process must only be one that adds value[9]. It is vital to understand where tasks are stuck and the causes of it to eliminate or reduce wasteful activities and achieve a smoother and improved flow of value to the end customer.
Several methods can be implemented to maintain a smooth flow of value-adding activities such as breaking down tasks, redesigning production systems, leveling workload, and skill-training employees[6].
4. Establish Pull
With smoother value stream flow, organizations can now provide improved time to market (TTM) and reduce inventory issues through a pull-based system. In other words, it allows customers the benefit of ‘pulling’ value (product or service) at the time they need it – a.k.a. “just in time” delivery and manufacturing. As such, organizations need not produce value in advance or stockpile products whilst increasing inventory. This creates a balance between the demand and production amount; hence, saving costs, time, and resources[9].
5. Seek Perfection (Continuous Improvement)
Now that the first 4 principles of Lean are accomplished, moving on to the fifth and final step is the most crucial one that must be done to successfully incorporate Lean thinking and process improvement into the organizational culture.
To seek perfection in business operations requires continuous improvement in the processes and a shift in culture within the organization. To illustrate, changes in the processes and operations from Lean implementation should not remain static and need continuous effort to improve by going through value stream mapping repeatedly in a way that is seeking a state of perfection (zero waste)[8]. This way, more and more hidden sub-process that cause waste can be detected and eliminated which helps in unlocking the full potential of the overall process.
TOOLS INTEGRATED WITH LEAN’S 5 PRINCIPLES
To implement the 5 Lean Principles effectively, multiple tools and techniques were designed and integrated into the principles. They include Value Stream Mapping (VSM), 5S, Kaizen, Error-Proofing (Poka-Yoke), Kanban, SMED, Takt Time, Root Cause Analysis, and Andon. These are some of the most commonly utilized Lean tools that provide better ways to define, investigate and reduce/eliminate wastage in the value stream flow.
APPLYING THE 5 LEAN PRINCIPLES IN YOUR ORGANIZATION
Having gained more knowledge about Lean, waste, and Lean’s 5 key principles, you can now apply these principles to improve your business operations and integrate Lean thinking into your organizational culture. These 5 Lean principles can guide you to establish an efficient value chain and eliminate inefficiencies and waste; thus, increasing customer satisfaction, work production, cost saving, and profitability.
INTERESTED TO LEARN MORE ABOUT LEAN & HOW IT CAN HELP YOUR BUSINESS?
Then, come and visit us at https://mbizm.com.my/for more information, or you can fill in your details and inquiries at: https://mbizm.com.my/contact-us/ and we’ll be there to get you started on your Lean journey!
Looking forward to having you onboard!
[continue in mbizm.com.my]
JOIN US!
Be a member at https://sixsigma.org.my/membership/ and receive various membership perks related to Lean Six Sigma – vouchers, discounts, networking, and more! For more information, visit us at https://sixsigma.org.my/
REFERENCES